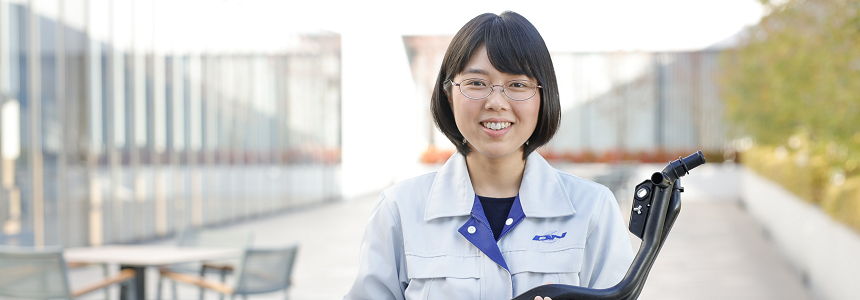
新たな工法で樹脂の可能性を広げる『冷却水パイプ』
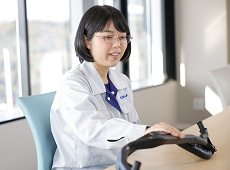
EV化が急速に進みつつある自動車業界の中で、当社ではEV用のパワートレイン部品の新規開発を進めています。EV化が進む中で電子部品など高熱を発する部品が増えているため、部品を冷却する水を流すパイプに焦点を当てて開発を進めることになりました。
従来の樹脂製パイプは、半割り状態の樹脂パイプを溶着する工法や、内側から空気を吹き込んで膨らませるブロー成形などで製作されています。今回は、「ガスインジェクション(INJ)成形」と呼ばれる工法で開発しました。
この工法は、溶かした樹脂を金型に流し入れた後にガスを吹き込んで内側の樹脂をくり抜くことで中空状のパイプを成形します。分岐や締結といった複雑化するパイプの形状に対応することが出来ます。
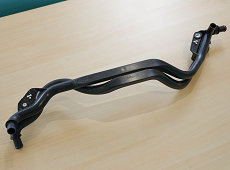
私が開発に携わった当初は冷却水パイプに対するガスINJ工法の知識がなかったため、基本的な勉強を行い、社内外の方からも学ばせていただきながら少しずつ技術力を向上させました。
冷却水パイプの開発を進めていく中で一番苦労したのが、パイプの内径の確保でした。ガスINJ成形では高温で溶かした樹脂を型内に流し入れるのですが、樹脂の温度が下がり固まることで、樹脂を注入した側の内径よりも出口側の内径が小さくなるという課題がありました。また、今回の製品は仕様上、楕円・四角形といった様々な断面形状になっており、複雑な形状を実現する必要がありました。
課題に対しては、設計や技術のメンバーと集まって対策案を出し合い、カーブの角度や形状をなめらかに変化させることでガスを流れやすくしたり、樹脂の条件を最適化することで解決していきました。
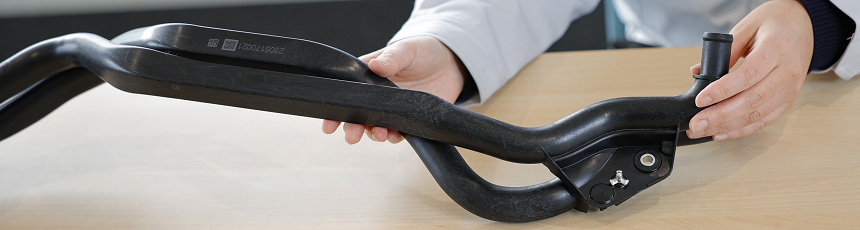
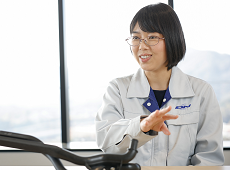
新製品を確実に量産につなげるため、R&Dであまり携わることのない量産前の工程までを担当しました。量産に向けては、成形・組立・検査などの工程でどのような設備や保証が必要なのか、技術のメンバーと検証、打合せを重ねながら進めました。また加工工程で発生する不要な樹脂を製品にリサイクルする仕組みを取り入れることで、歩留まり100%を実現することができました。
今回の開発を通して、冷却水パイプの技術を確立できただけでなく、量産工程の立ち上げまでを学び、社内外のたくさんの方とのつながりを構築することができました。
現在はガスINJ成形を応用した新工法の開発にチャレンジしています。ガスINJ成形では難しかった長尺のパイプを実現するため、この工法もしっかり量産につなげられるように頑張ります。