Shift to computerized-verification-oriented development supporting product strategy
Given that, in recent years, the functions required of automobiles have become more and more advanced and diversified, eligible vehicle structures and control systems are forced to be increasingly complex, and this will continue to accelerate in the future. To keep developing such complex systems quickly and with limited resources, Model-Based Development (MBD), enabling efficient development by computer, is essential. DaikyoNishikawa promotes co-creation by MBD in collaboration with business partners and in an industry-academia-government collaboration. Model-Based Development aims to shorten the development period by reducing the number of vehicle-level evaluations and prototypes by utilizing computerized simulations. To achieve these goals, we are innovating our development process and CAE* analysis technology.
* CAE: computer aided engineering
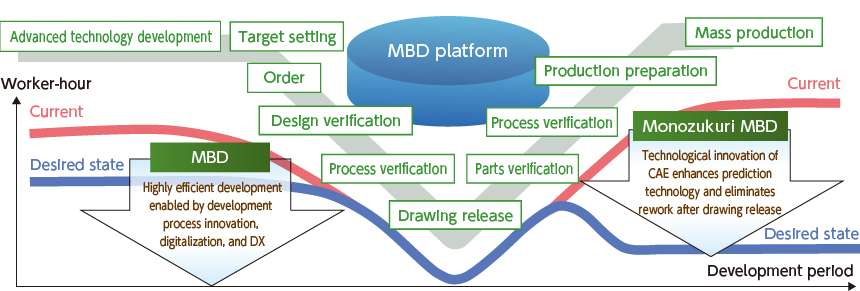
Activity Examples
Rigidity/Vibration Analysis
Bumpers are one of the largest plastic parts and require high levels of rigidity, impact resistance, and appearance quality.
To satisfy individual functional requirements, accurate CAE analyses are required. Rigidity provides basic product functions. By raising the accuracy of rigidity analysis, we are working to optimize the structure and reduce weight while ensuring other functions.
Impact Analysis
Automotive safety technology is broadly divided into preventive safety technology intended to avoid accidents and collision safety technology that reduces damage in the event of an accident. Our in-house produced instrument panels feature a structure that absorbs the impact force applied to the occupant's head in the event of a collision to provide improved occupant protection performance. We use impact analysis with improved accuracy thanks to computer-based predictions to develop a lightweight, optimal structure while ensuring safety.
Air Conditioning Analysis/Thermal Management
As vehicles are increasingly electrified to achieve carbon neutrality, thermal management is also undergoing major changes. The cabin needs to create an optimal space with minimum power consumption. In addition to the current technology for predicting the flow of air, we are working on analysis technology used to visualize temperature changes in the interior space and to evaluate heat transfer and the effects on it of our products.
Plastic Flow/Warp Analysis
Injection-molded plastic parts are subject to deformation due to thermal shrinkage occurring inside the mold and after removal, which greatly affects the product quality. Therefore, we are working on technological innovation to reproduce, and control, what takes place in the machine by CAE analysis, which, more specifically, visualizes the flow of plastic and thermal changes in the mold and clarifies the mechanism.
We started verification using this analysis technology for product development in FY2022 onwards.