The cockpit—an interface between the vehicle and the driver & passengers—is important not only for safety, but also for creating a space that multiplies the comfort and enjoyment of driving many times over. We bring out the potential of plastics and help create a luxurious and comfortable space.
Instrument Panel
Exquisite touch and feel of powder slush molded PVC (Polyvinyl Chloride) surfaces enabled by DNC's original material development
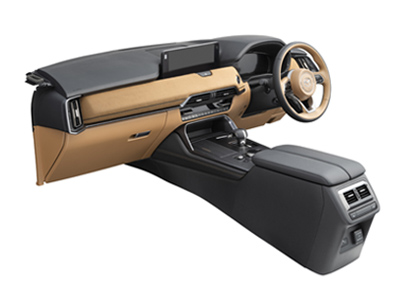
Simultaneous development of a PVC powder slush molding material and a urethane foam material was intended to create the ideal touch and feel. We have achieved a comfortable tactile impression that appeals to the senses. In addition, for the front passenger airbag, an invisible airbag structure has been adopted to impart an improved appearance. This structure, unlike the conventional separate structure between the airbag and the lid, is integrated with the instrument panel so as to hide the parting line of the airbag deployment opening in front of the front passenger seat to the effect that the equipment is inconspicuous. Furthermore, having evaluated airbag deployment performance in-house, we have fulfilled both appearance and safety requirements.
Slush Molded Surface Sewing Technology
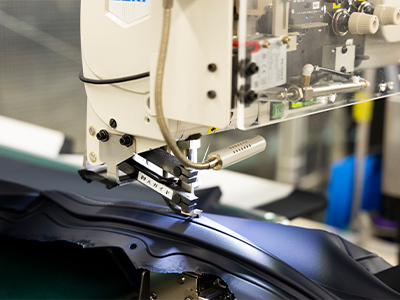
We supply customers with instrument panels provided with real stitches. This was made possible through research and development pursued to apply stitches so that thin PVC surfaces powder-slush-molded into a three-dimensional style would look carefully crafted. It was success in stably applying real stitch lines even on a material that stretches and tears more easily than fabrics. The key to the success was incorporation of our proprietary expertise into industrial sewing machines to meet the needs of the market and customers who demand a more authentic feel. Moreover, we have designed a process that can automatically distinguish various thread colors, enabling high-mix low-volume production and inventory optimization.
Decoration Panel
Prototypes verified at the development stage facilitate design flexibility.
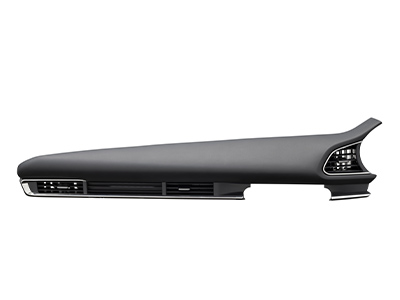
To reproduce a higher level of texture, it is necessary to design a sophisticated form.
Leveraging our technical expertise built through experience in upholstering, we make development efforts so as to faithfully reproduce the designed form.
Rear Console
The ideal way of opening and closing the console lid achieved based on how users actually use it
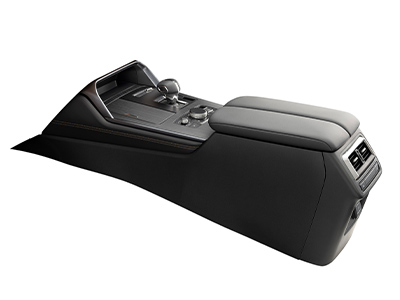
What we have developed is not limited to the function of providing support to the passengers. We have developed a structure that is sufficiently rigid for intuitive operation and is extremely user-friendly. In addition, the product design has also pursued quality (comfortable tactile sensation).
Indicators
Integrated development of electronic parts and plastic parts enabling mass production of electrical parts
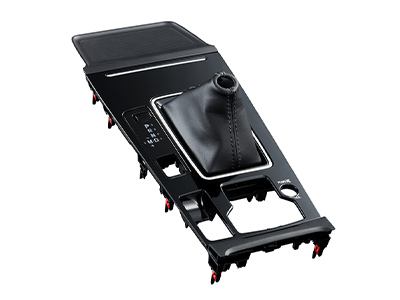
In 2019 DaikyoNishikawa began to mass-produce gear shift indicators for automobiles. The basic technology used in them was a microcontroller equipped with a single integrated circuit comprising communication between multiple Electronic Control Units (ECUs) and Light Emitting Diode (LED) control. The gear shift indicator is also equipped with a circuit that minimizes standby current.
Integrated development of electronic parts and plastic parts has enabled us to develop parts that are stylish and offers uniform aesthetic quality.
Electronic Parts Development Technology
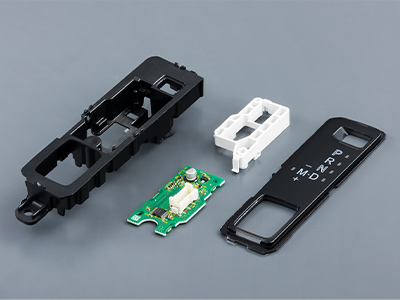
In 2016, with the advent of CASE, DaikyoNishikawa began full-scale development of automotive electronic parts to take on challenges in an area new to the Company.
Comprehensive development spanning from mechanism/circuit/software design to mass production enables the Company to improve the quality and speed of its development approach meeting market needs and to develop products that combine its unique technology with electronic technology.