Many of our products are also used in the front end, which is the "face" of a car. We develop products focusing not only on visible areas but also on areas that are usually invisible. Safety, harmonization with the body, creation of an impressive car expression, and weight reduction and other improvements in environmental performance are also important factors in our product development.
Bumper
Environmental friendliness using a non-degreasing painting method
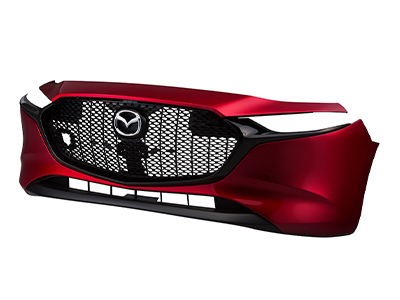
We were among the first to develop a non-degreasing method that does not require trichloroethane, an organic solvent. This eco-friendly painting method is used for our manufacturing. We can develop and produce bumper modules that contain reinforcements. Furthermore, having adopted a talc masterbatch production method for in-house production of plastic materials, competitive and efficient manufacturing has become possible.
Radiator Grille
High quality and low cost owing to the use of bio-polycarbonate (plant-derived raw material), eliminating the need for painting
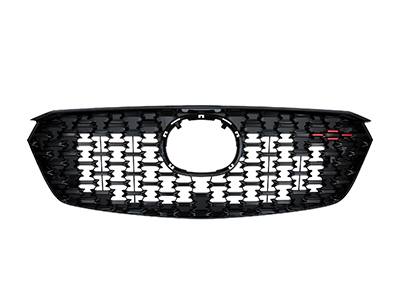
We have reproduced a mirror-like smoothness and a deep color that surpass conventional piano black painted parts, while the cost has been reduced by omitting painting. We have a track record of mass-producing many exterior and interior parts such as radiator grilles and switch panels. By creating products using renewable plant-derived raw materials, we will help build a recycling-oriented society and offer a high level of eco-friendliness and appearance, adding even higher value to our products.
Shroud Panel
Modularization and weight reduction of parts using long-fiberglass reinforced plastic
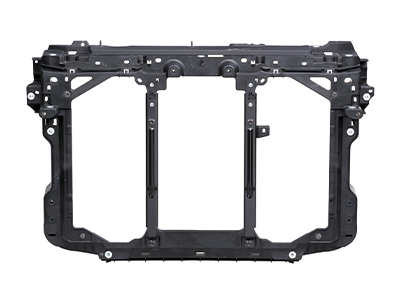
The radiator support structure made of plastic, contributing to weight reduction, has improved vehicle performance and fuel economy. Moreover, reduced aerodynamic drag and the use of an active grille shutter effectively working to efficiently raise the engine temperature during engine start-up help further improve the fuel economy.