Biopolycarbonate
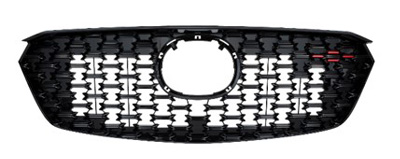
Use of Bio-based Engineering Plastics in Radiator Grilles
Using our proprietary technology, two-color/-material molding at the material stage, we have eliminated the painting process and have achieved reductions in environmental impact and costs.
The use of plant-derived raw materials helps reduce the consumption of petroleum resources and CO2 emissions.
Cellulose Nanofiber (CNF)
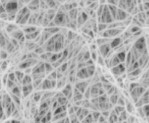
Cellulose Nanofiber (CNF)
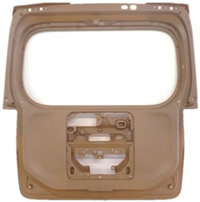
Tailgate Inner Panel Made of 30% CNF-Mixed Polypropylene
Cellulose nanofibers are suitable for reuse because they retain strength relatively well even after they are recycled, making them a material that can contribute to a recycling-oriented society.
Participating in a program organized by the Ministry of the Environment, the Government of Japan, we are promoting research and development to create materials, molding methods, and products that take advantage of the features of cellulose nanofibers: low specific gravity, high rigidity, and low linear expansion.
Establishment of Foam Molding Methods
We manufacture products while significantly reducing the amount of materials used owing to proprietary materials and foam molding developed in-house.
Foam molding is a method that features creating air cells filled inside the molded product.
The method enables us to increase the thickness of the product with a minimum amount of plastic for achieving both weight reduction and high rigidity.
As development efforts for further adding value to our product, our ongoing research includes improving heat insulation by forming finer foam cells.
Replacing Metal with Plastics
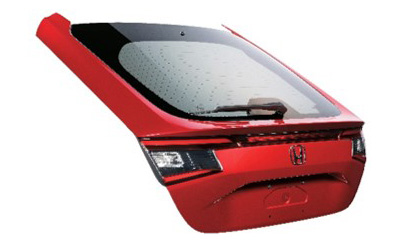
Plastic Tailgate
Our plastic tailgates are about 30% lighter than those made of steel and have enabled cost reductions owing to a reduced number of parts made possible by in-house plastic materials and proprietary engineering methods.
We are making development efforts to improve functions, add more value, and reduce costs to roll out our products to more vehicle models.
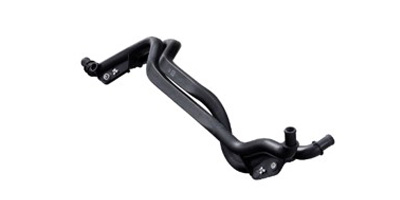
Plastic Cooling Pipes
Gas-assisted injection molding is the method of forming a hollow body by, after filling the mold with plastic, pushing out the internal unsolidified portion with a high-pressure gas. The gas-assisted injection molding method makes the product about 40% lighter than products made of metal.
Furthermore, with the aim of reducing material waste to zero, we have incorporated in-process recycling of unused portions and IoT-based quality control focusing on optimum-quality conditions, thus achieving a 100% non-defective rate. Moreover, by eliminating highly difficult direct work, we have made it possible to reduce defects due to human errors to zero.