We pursue a Monozukuri environment that will precisely meet customer requests. It comprises the cell production and assembly method that flexibly designs the assembly process according to the product specifications and quantity, the fully automatic assembly method that realizes stable quality, and the teamwork assembly method intended to swiftly manufacture identical products. The goal of these methods is to efficiently implement model-mixed scheduled sequential production as demanded by our customers.
Model-Mixed Scheduled Sequential Production
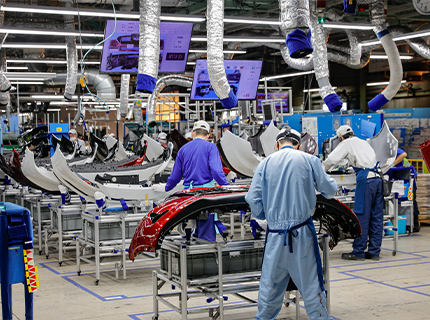
Mazda Motor Corporation—our major customer—adopts scheduled orderly production in which they produce cars in the order they have been ordered. We are in line with the scheduled orderly production. We have built a system that enables prompt delivery while reducing inventories even in the case of diversification of vehicle types and options.
Cell Assembly
One person carries out all the assembly steps; the cell assembly system is a form of Monozukuri that thoroughly eliminates waste arising from layaway and teamwork.
It is the ideal assembly method for accommodating fluctuations in production volume and for model-mixed scheduled sequential production.
Using the cell assembly method, the operator develops a sense of responsibility and mission in Monozukuri completed by a single person; at the same time, he or she feels the joy of Monozukuri.
Teamwork Assembly
Teamwork assembly is an assembly method in which one product unit is completed by several operators. In this method, several people share work elements in assembly and become skilled in their respective jobs with ease. It is an effective assembly method for assembling a large volume of the same product. Continually constructing the same product provides the advantage of making the assembly faster. The method is also suitable for training multi-skilled workers because it permits changing the number of parts assigned to individual work portions.
Assembly Synchronized with Molding
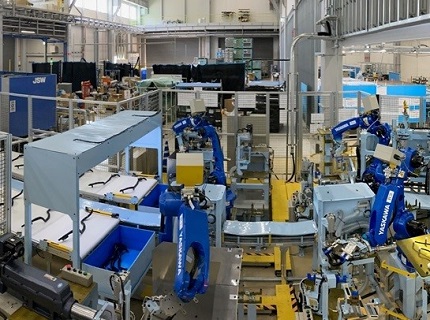
Assembly synchronized with molding refers to the method of assembling molded parts on the spot. It eliminates work-in-process inventory between molding and assembly and therefore is a production method essential for straight production and streamlining.
With conventional molding, a large volume of products are molded at once and supplied to the following process, requiring provision of space for temporary storage of inventory. However, assembly synchronized with molding when established will eliminate the need for work-in-process inventory and make it possible to significantly reduce inventory space.
Tailgate Assembly
Plastic Tailgates contribute greatly to vehicle weight reduction and environmental conservation compared to conventional steel ones. We assemble Tailgates efficiently and functionally with the synergy effect between man and machine. A new engineering method incorporating automated degreasing, primer application, and bonding of outer parts provides stable quality and saves space. A finished Tailgate is called a Tailgate module, which is delivered to the customer in a state whereby it can be attached to the vehicle body as it is. Accordingly, it reduces the number of assembly steps required on the vehicle body.
Unmanned Assembly
Unmanned manufacturing is a human-friendly form of Monozukuri. The elimination of human intervention will avoid human errors and contribute to the stabilization of quality. Take the example of the product called the assist grip. As soon as its parts are molded, several robots assemble them fully automatically. We have established unmanned systems that include checks for missing parts,8 performance inspection of assembled parts, and checks for wrong parts.9
Another example is airbag case production, which is synchronized with molding; inspections and loading of racks with finished products are also unmanned.
8. Missing parts: parts left unattached
9. Wrong parts: mixing of different parts