Monozukuri is
Human Resource Development
Manufacturing
DNPS
The DaikyoNishikawa Production System (DNPS) is an activity that involves
all employees in thorough pursuit of value thereby realizing the ideas of
value formation and just on time at a high level and giving each production
staff member the ability to make profits. Based on the concept of just on
time, we increase value by standardizing all work in Monozukuri in terms of
both people and equipment, and we have realized model-mixed scheduled
sequential production1 centering on straight production.
In addition, DNPS activities set five targets: “safety and security,”
“environment,” “quality,” “delivery,” and “productivity.” We believe that
the process of pursuing these targets will greatly facilitate the growth of
each employee, enabling development of human resources embracing better
ideas. By acting while leveraging the way of thinking acquired through these
activities, we are realizing One Best Way.
1. Model-mixed scheduled sequential production: To produce various vehicle
models in an established order
Click here for details
Monozukuri
Molding

A heated plastic material is injected into molds of various shapes and
then cooled. In this way, plastic products of a wide variety of shapes
can be molded. Various molding techniques such as injection,
compression, blow, powder slush, and polyurethane injection are used to
pursue Monozukuri that meets customer needs and to conduct eco-friendly
manufacturing.
Click here for details
Painting
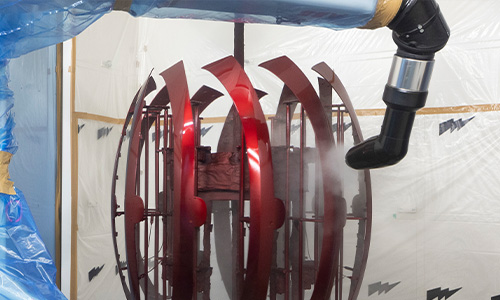
The painting process receives materials from the previous process—the
molding process—and increases the value of products by painting them,
achieving both quality and environmental requirements and meeting
diverse customer needs. We have realized unmanned painting equipment
using a spindle method tailored to automotive large parts, electrostatic
painting, and painting robots, which improve painting efficiency. We
also offer premium colors with high quality even though they are
difficult-to-achieve paint colors.
Click here for details
Assembly
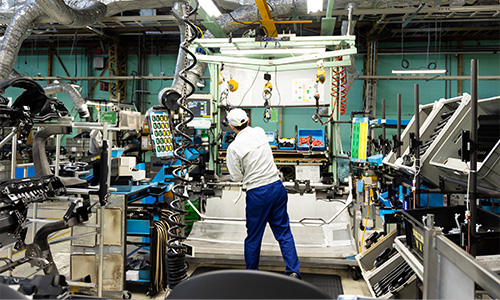
Assembly is the worksite that is the closest to our customers.
Model-mixed scheduled sequential assembly is realized tailored to
customer requirements. The assembly process assembles more than 80 parts
at the most, by methods such as bolting,2 fitting,3
affixing, and insertion, to name a few. Our Monozukuri is safe and
efficient, combining human-friendly unmanned assembly, the introduction
of collaborative robots, development of processes with clear criteria
for work difficulty, and ergonomics4 evaluation. In addition,
to be in line with customer needs, we select a production system from
cell, lot, AGV (Automatic Guided Vehicle), and other production systems.
Our goal is to assemble and deliver products to our customers on a
just-on-time basis (delivering when and what is needed and in the
precise amount needed).
2. Bolting: to tighten with threaded fasteners
3. Fitting: to mate parts
4. Ergonomics: human engineering
Click here for details
Kaizen (Improvement)
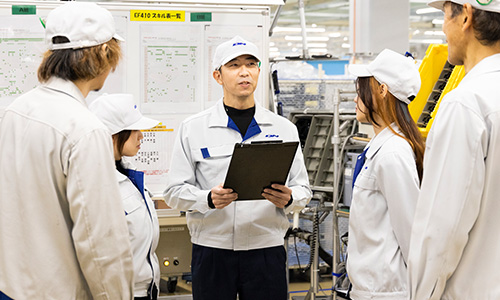
To achieve the desired state in small groups, we note the difference
between the current state and the desired state (ideal model) of the
worksite and formulate strategies, identify problems, clarify issues,
and promote Kaizen activities to resolve the difference.
Click here for details